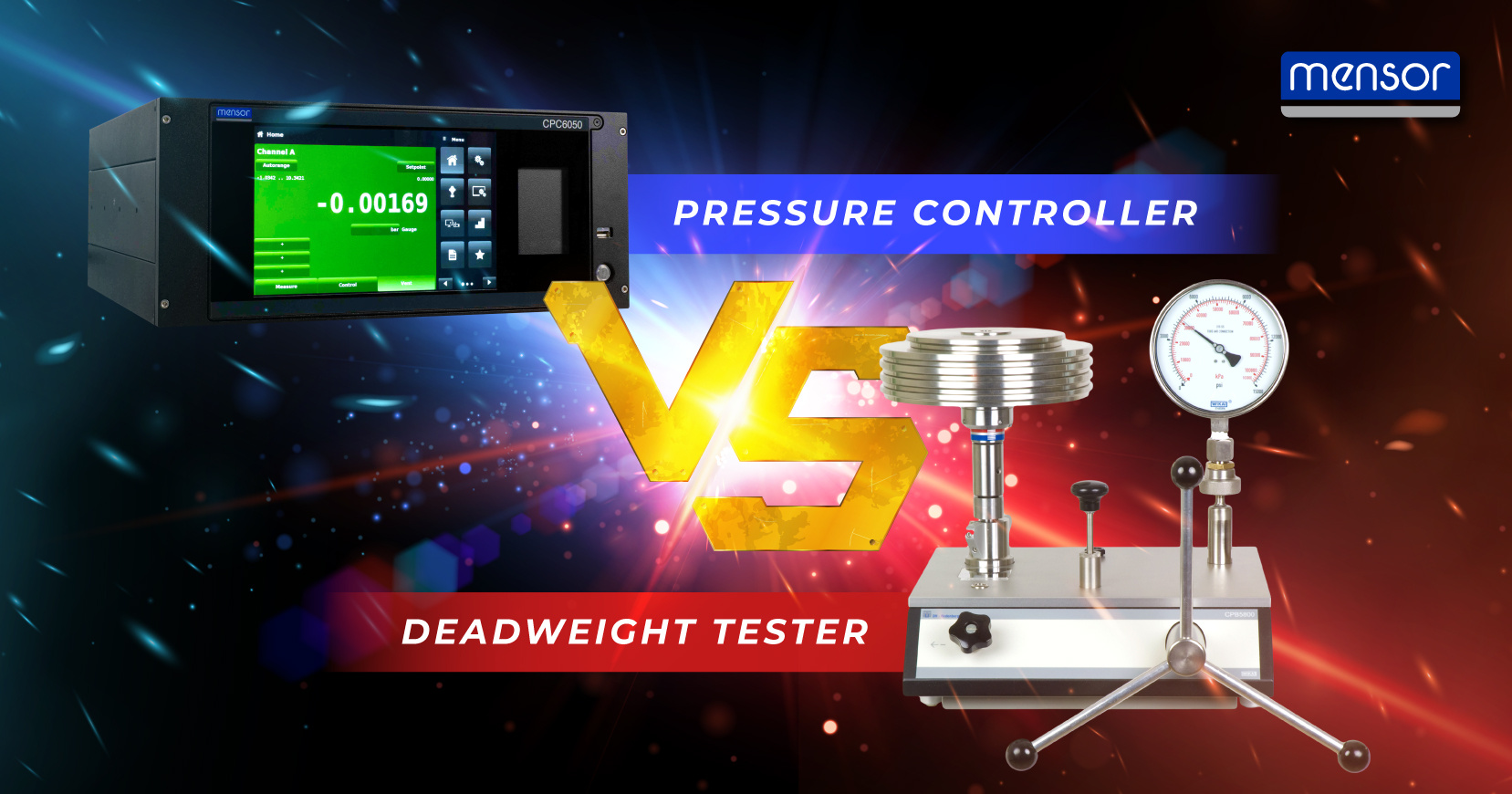
As automated processes revolutionize the world of metrology, there's a growing debate that manual deadweight testers are troublesome and in need of updates. Heavy external mass loading, separate environmental calculations, and slower calibration time may justify these concerns. If pressure controllers can accurately measure pressure in seconds, why would we still want to use deadweight testers? In this blog, we'll explore deadweight testers' role and impact on metrology.
What are deadweight testers?
Deadweight testers calibrate pressure-measuring instruments by applying calibrated masses over a piston area. The medium under the piston is increased in pressure to ‘float’ the piston. The goal is to establish an equilibrium between the known reference pressure and the DUT (Device Under Test). Due to their SI unit-based measuring principle and lack of electrical components, deadweight testers are regarded as one of the most precise and traceable pressure-measuring instruments available. They are most beneficial to industries requiring higher accuracies and traceability. For instance, deadweight testers with portable and durable designs would be perfect for quality assurance processes such as power plants and maintenance facilities.
What are primary standards?
The International Vocabulary of Metrology defines primary standards as measurement standards that establish their quantity value and measurement uncertainty using a primary measurement procedure. In other words, a primary instrument is used as a standard reference to calibrate DUTs. Deadweight testers are the first to come to mind when referring to primary pressure standards. However, it's important to remember that some industries define primary pressure standards differently.
Advantages
There are many advantages to using a deadweight tester for calibration. They use mass and a stable piston and cylinder system to create pressure, providing consistent and traceable results. Various options are also available to accommodate different DUTs, environments, and pressure ranges. One can choose pneumatic or hydraulic deadweight testers, as well as digital or manual ones. The deadweight tester calibration covers low, mid, and high-pressure levels.
Disadvantages
Of course, some drawbacks must be addressed. Deadweight testers can not compete with fast pressure controllers, such as the CPC3050. While the precision is unmatched, they're not ideal for industries prioritizing speed over higher accuracies. Factors such as gravity, the piston's temperature, and barometric pressure can also affect the pressure calculations. These environmental conditions need to be factored into the equation. Finally, more labor is involved than automated processes, such as spinning the masses and waiting for stabilization, all for only one reading.
But how do they compare to automated calibration instruments like pressure controllers?
Pressure Controllers or Deadweight Testers?
As pressure controllers advance in speed and accuracy, selecting one over a deadweight tester seems obvious. After all, they can serve as interchangeable reference standards depending on the industry. Automation, convenience, and accessibility are strong selling points for a controller. Additionally, having multiple pressure ranges and different accuracy classes within one device is advantageous. However, while end-of-line testing and transducer characterization can be automated through remote software and computer programs, the user must depend on a digital reading. A pressure controller's electronic and remote aspects can introduce more uncertainty than a traditional primary standard.
The accuracy and reliability of deadweight testers stem from their use of fundamental physics principles. Their durability and minimal drift error allow them to maintain trusted calculations and historical data for years. It's clear why they have been a cornerstone for primary standards for so long. Instead of being seen as old-fashioned and cumbersome, perhaps deadweight testers should be regarded as the tried-and-true method for calibration.
So, after reviewing the pros and cons of deadweight testers, one question remains: Are manual deadweight testers still relevant? Unfortunately, there's no straightforward answer; it depends on the specific applications and industries. For instance, a calibration lab seeking traceability and the utmost measurement certainty should have a primary standard. On the other hand, pressure controllers are the optimal choice for production lines that necessitate swift and efficient automatic testing.
As pressure instruments evolve to meet the demands of the modern world, deadweight testers continue to be a dependable method for high-precision pressure measurements. With the increasing accessibility of advancements such as digital deadweight testers, it is evident that they will continue to be essential for many years to come.
FAQs
- What are the main components of a deadweight tester?
The main components of a deadweight tester typically include:
- A piston-cylinder assembly
- A set of calibrated masses
- A pressure generation system (often a screw press)
- Valves for controlling pressure
- A base unit with leveling adjustments
- A precision temperature probe for measuring piston/cylinder temperature
- How do I know which pressure instrument I should pick?
Selecting the appropriate pressure instrument depends on several key factors: the required pressure range, accuracy needs, the medium being measured (gas or liquid), environmental conditions of use, compatibility with the measured substance, portability requirements, budget constraints, ease of use, and maintenance considerations. By carefully evaluating these aspects, you can choose an instrument that best fits your specific application, balancing precision, practicality, and cost-effectiveness. It's important to consider both immediate needs and long-term factors like calibration frequency to ensure the selected instrument will serve its purpose effectively over time.
- In what ways are digital deadweight testers different from traditional deadweight testers, and how might they impact their continued use in metrology?
Digital deadweight testers differ from traditional ones by using electronic sensors, offering advantages in ease of use, portability, automation, and range coverage. They're less affected by environmental factors but require periodic calibration. In metrology, digital testers are increasingly adopted in industrial and field settings due to their convenience, while traditional testers remain important as primary standards. The rise of digital testers may impact training requirements, cost considerations, and discussions on traceability. As technology advances, digital testers may challenge traditional ones in high-precision applications. Still, both types are likely to coexist in the foreseeable future, each serving specific roles in the field of metrology.
Learn more about Pressure Controllers AND Deadweight testers by tuning into
Mensor's Podcast, Measure Matters!
Like and Follow for More!