Choosing a digital pressure gauge can be difficult if you're not clear on the subtle differences between various types. A digital pressure gauge (DPG) is defined here as any pressure measurement device that indicates pressure digitally using an electronic display. A DPG is presented in contrast to a dial gauge that uses a purely mechanical component to sense and indicate the pressure. Dial gauges have been used for a long time in industry. They typically indicate pressure using a Bourdon tube, which is mechanically linked to a dial that rotates on a graduated circular scale.
These are designed to give a local, visual indication of the pressure in a process but typically do not provide a way to transmit the reading. This type of mechanical dial gauges may be suitable for your application, but they have a few inherent drawbacks. These include mechanical wear, difficult to read dials, lower accuracy (typically 1.0% to 5.0% FS), and some susceptibility to mechanical vibration. The advantages is their low cost and that they do not require any power and, therefore, are safe to use in hazardous environments.
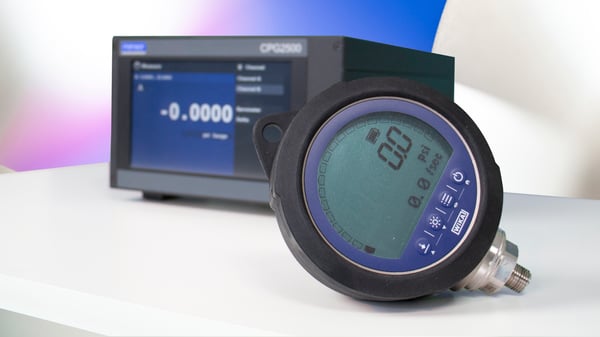
This article describes some reasons why a digital pressure gauge may be a better choice for your application. We will discuss two main categories and, for the purpose of identifying them, we will call one a digital dial gauge and the other a digital pressure indicator.
Digital Dial Gauge
A digital dial gauge is a DPG that looks like a traditional dial gauge in that it has an integral process connection and a round case with a display on the front. However, in place of the mechanical workings, it contains a pressure transducer and electronics that can digitally display a high resolution pressure reading. The display may be backlit and include various pressure related data collection and display functions, including data logging, min/max display, peak alarms, units selection, temperature readout, tare function and more. Taking advantage of the onboard electronics, the gauge is also capable of remote data transmission. When the gauge is to be used in a hazardous environment, intrinsically safe certifications are available. This type of DPG usually has an accuracy class from 0.02% to 0.5% FS and ranges can be as low as 10 inches of water to 150,000 psi.
Digital Pressure Indicators
Digital pressure indicators are typically available in a desktop or rack mounted case. The case may have one or multiple internal pressure sensors with individual pressure connections and a programmable display showing one or all of the pressure readings and various auxiliary functions. These typically use pressure rated tubing to connect to the process or test port being monitored. They may also be capable of communicating and displaying the readings of one or more remotely mounted pressure transducers. They can have a variety of functions that exceed the capabilities of the digital dial gauges described above. They are easily connected to external systems for data exchange using RS-232, IEEE-488, USB or Ethernet. Settings in these devices control the display appearance, units selection, pressure signal transmission settings, resolution, and adjustments to other pressure related functions. Emulation of pressure types can be achieved by using an internal barometer, and emulation of differential pressure using two internal sensors is possible in some models. This type of DPG is usually equipped with transducers in an accuracy class between 0.01% FS up to 0.008% R, with ranges as low as 10 inches of water up to 10,000 psi.
Now that the subtleties between digital dial gauges and digital pressure indicators have been explained, application-based reasons to choose between the two, as well as applications where either may be acceptable are described below.
Continuous Process Monitoring
For direct single point continuous process monitoring a digital dial gauge is a good choice. A process pipeline, tank or any pressurized vessel containing liquid or gas may require an accurate, high resolution, local indication of pressure. A digital dial gauge can be connected directly to the process at the location of interest. Large digital displays with backlit screens will minimize reading error. Digital dial gauges may also provide wireless or electronic communication for remote monitoring or data collection.
Transfer Standards or Calibration Reference Standards
A digital pressure indicator can be calibrated using a laboratory standard on a regular basis and then used as a portable "transfer standard" to verify the readings of a field standard or portable pressure calibrator. A digital pressure indicator might be the best type of DPG to use in this application because they are usually equipped with high accuracy transducers and the capability of having multiple ranges, especially if they are equipped with interchangeable sensors.
For calibration purposes, either type of DPG can be used. However, in calibration, a source of regulated pressure must be available as well as a way to read the output of the device being tested. If a mechanical gauge is being calibrated, a simple comparison of the readings would suffice. A digital dial gauge can be equipped with a hydraulic or pneumatic pump to act as the pressure source. However, there are many multi-function field pressure calibrators that have pressure sensing, pressure generation and signal measurement incorporated. These types of portable pressure calibrators are used for field calibration in hazardous and non-hazardous environments.
Test Bench Applications
Either type of digital pressure gauge can be used successfully in a calibration test bench. Depending on the ranges that need to be tested or calibrated and design preferences, a test bench can take many forms. A bench might include digital dial gauges or digital pressure indicators, in addition to process signal measurement instruments, pressure pumps, pressure controllers and manifold, valves and software integration. The test bench shown here uses several digital pressure gauges of different ranges to provide a discrete calibration channel for the device under test.
After taking the differences in digital pressure gauges and various applications into account, below are the top five things to consider when choosing a digital pressure gauge:
- Range and Accuracy: Make sure both the range and accuracy class that you choose is adequate for your application.
- Materials: The DPG materials of construction should be compatible with the medium used in your application.
- Features: Examine the feature set to see if they match your expectations and application. Check features like communication protocols for remote monitoring, digital screen and number size, back lighting, min/max monitoring, data logging, etc.
- Environment: The ingress protection (IP) rating and hazardous location rating for explosive environments should be compatible with your application.
- Connection Compatibility: Pressure fittings should be compatible or adaptable to existing process connections.
Related Reading: